Main Product Features
User Interface (UI)
Modern and Fast in the Browser
CAD assemblies with +1,000s of surfaces handled in seconds.
Easy-to-use, top-down panels system for fast model setup.
Intelligent warning / error checks on data input and setup logic.
Auto-meshing workflow with small feature suppression for best mesh quality.
Generic couplings (soft & rigid) and spring elements for complex assemblies with realistic constraints and joint stiffness.
Parallel UI task computing, plus a Jobs Monitor to follow solving progress on each.
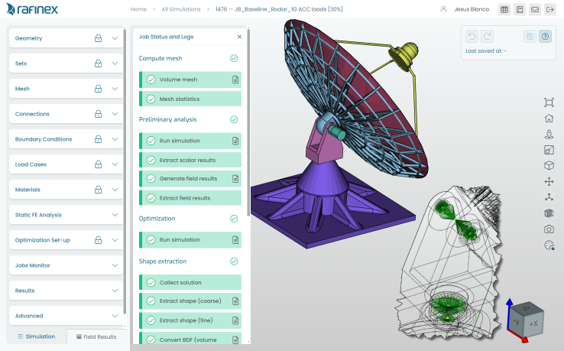
Fast Workflows – Templating
Intelligent “Import Setup” feature to apply templates based on colored sets from CAD model, or surface set names in the UI.
Fully automated workflow for shape extraction plus FEA validation setup and solve (TET10).
Easy download of results: STL, Nastran & Abaqus input deck setups.
The “Model Editor” allows for custom hand edits to experiment with unusual TO solver settings or to test newly added solver features before they are available in the UI.
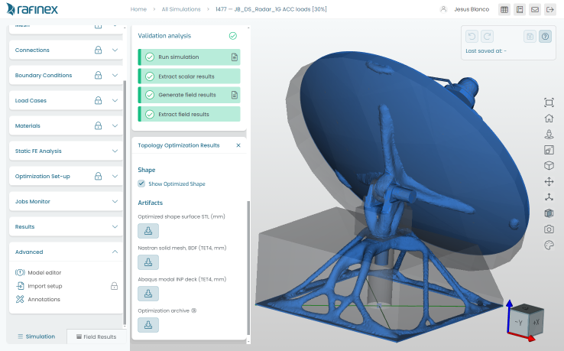
Results Viewer
FEA results for both preliminary (TO set up check) and validation (shape) analyses are carried out in the browser UI environment.
A Summary load case is generated on top of the user’s load cases, to show MAX von Mises levels, and worst (‘killer’) load cases.
In addition to the usual 3D contour results, Möbius generates an FEA text results file (CSV) to allow for fast & informed decision-making across many design variants based on graphs comparing stiffness, total strain energy or other metrics.
The CSV results are key to assess large assemblies with many parts.
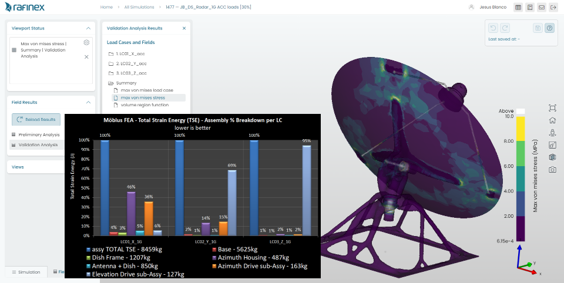
Solver
Modern Maths = Robust Designs
Möbius solver has been built on top of modern optimization algorithms and maths in conjunction with a powerful cloud solving infrastructure.
The solver scales when challenging applications are required. Solving optimizations with 25 million tet meshes is not a problem.
Special attention has been given to main TO constraints: casting, member size, overhang, symmetry and keep thickness (on surface sets).
The solver features an adaptive re-meshing technique, which increases detail during the optimization, but only where is matters.
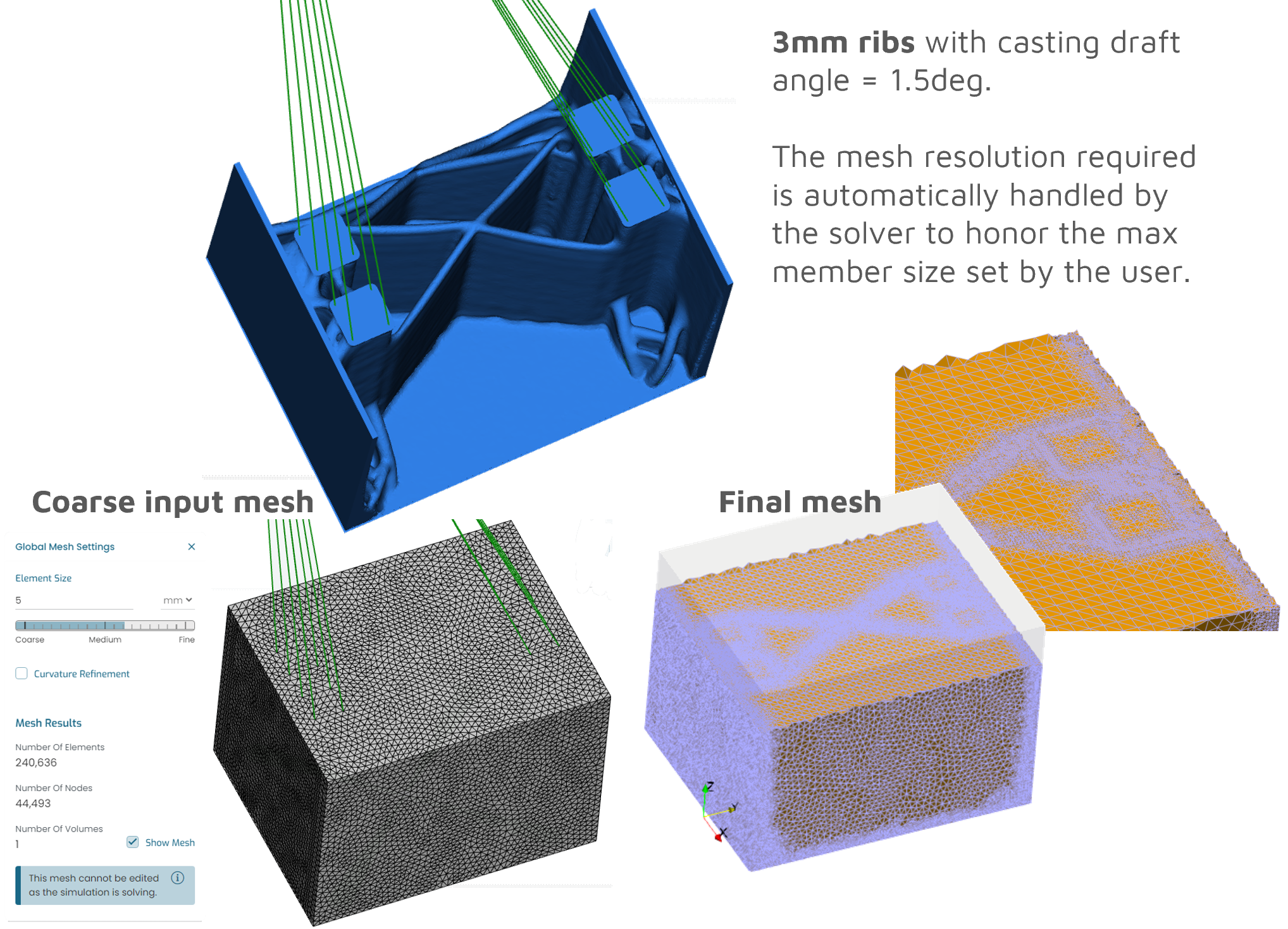
Multi-Axis Constraints
The ability to optimize assemblies also comes with TO constraints such as casting and symmetry in different axis directions (per part).
In this way, while complex assembly structural connections remain active, the solver is able to adapt to difficult manufacturing constraints.
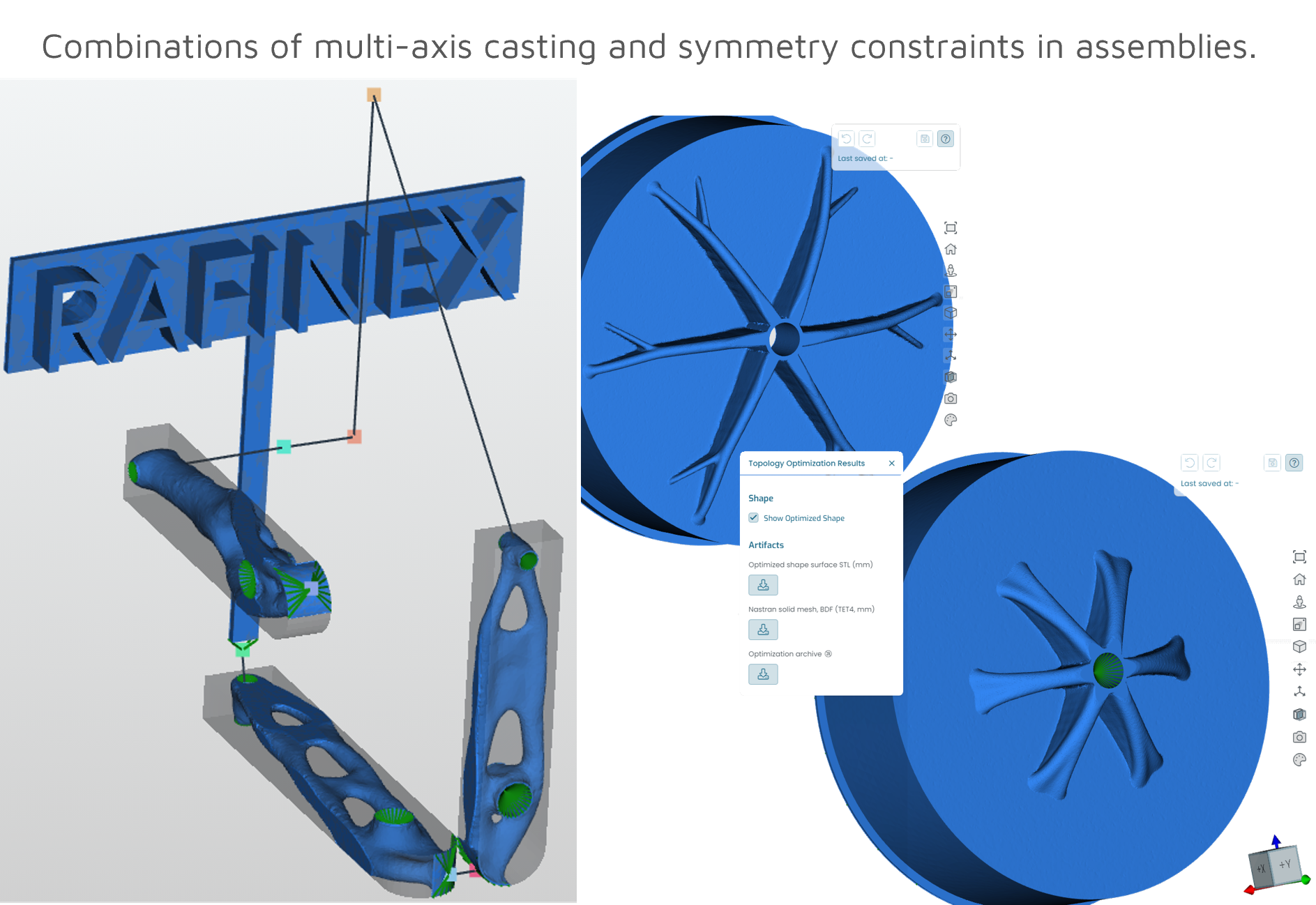
Multi-Material Optimization
When optimizing assemblies at design concept stage, it is desirable to assess how much mass should be distributed across separate key parts, while taking into account different materials for combined (assembly) stiffness.
Möbius allows seamlessly to solve for multi-material optimization.
It is invaluable to understand at the start of an assembly design: mass distribution and potential use of different materials, while keeping a check on structural performance as a whole, in addition to a per part basis.
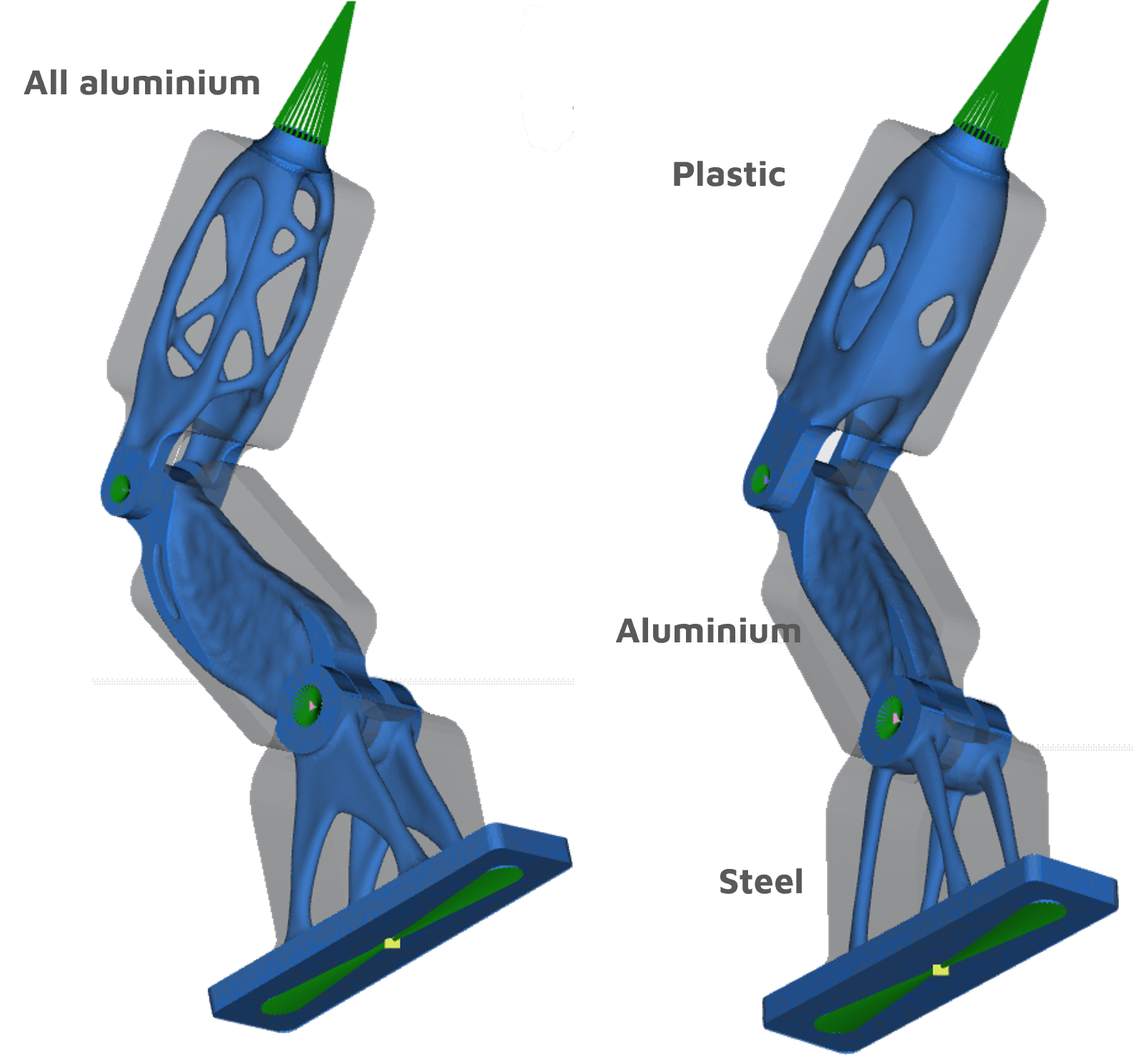
Upcoming features – 2024
User interface
Automated generation of fasteners (bolted, riveted), joints and bearings for accurate assembly setups.
Automated graph generation of FEA validation metrics for fast & informed decision-making across many designs.
Solver
Anisotropic materials: both for maximize stiffness and/or optimization of fiber directions.
Stress based Topology Optimization: minimize mass.
Automatic removal during solve of sharp corners from the design space CAD, when stress limits are of relevance.
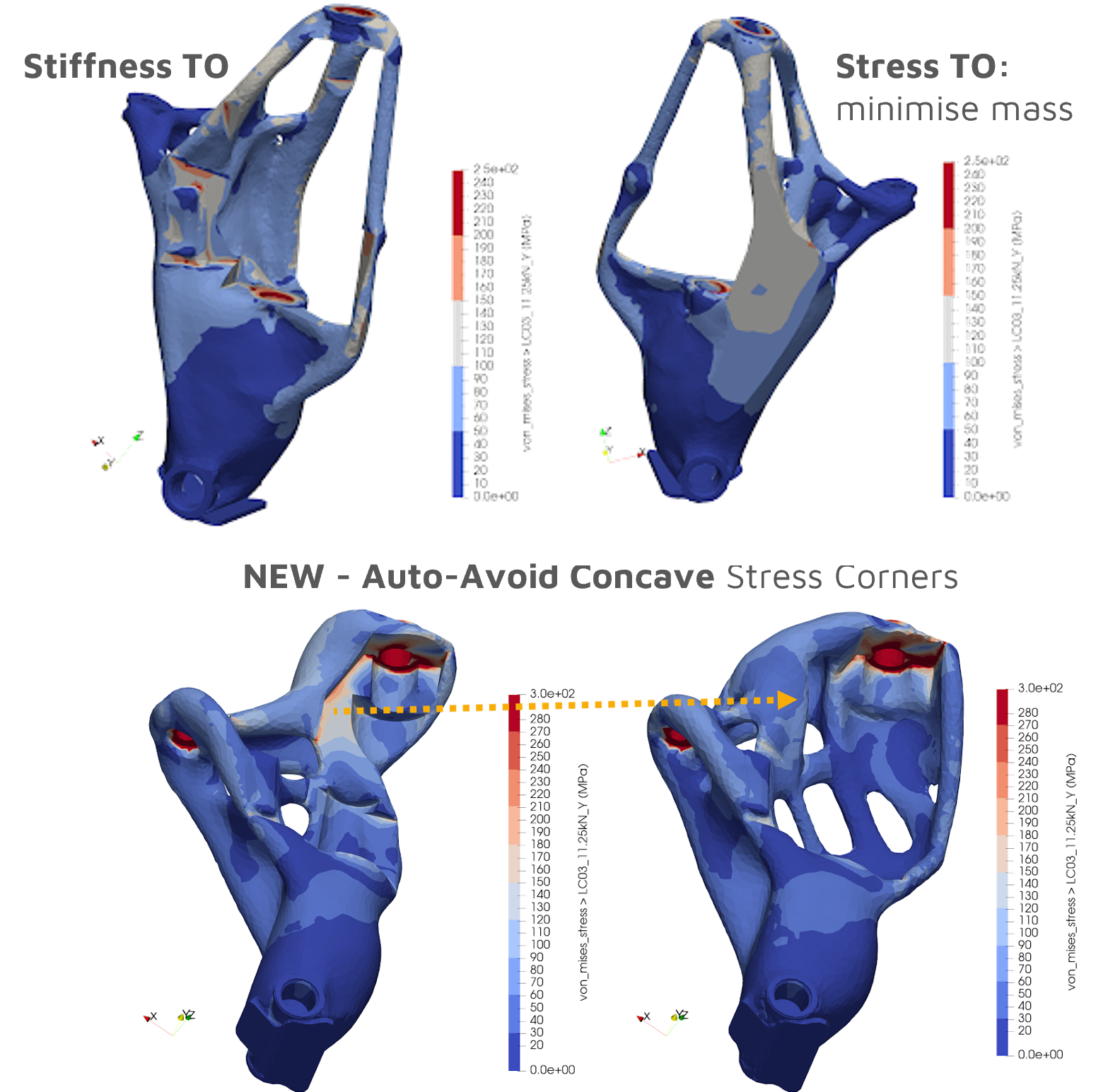
Roadmap - 2024
H1 2024 – Release of an entire upgrade of the optimizer kernel (Name: CALM) including higher-mesh resolutions and better constraints’ convergence.
H1 2024 – Public release of + 1TB of RAM optimization compute environments (+25M elements).
H2 2024 – Stress-targeted optimizer release (Global & Local Stress).
H2 2024 – Synera connector node.
H2 2024 – Frequency / eigenmode analysis as part of the FEA Validation.